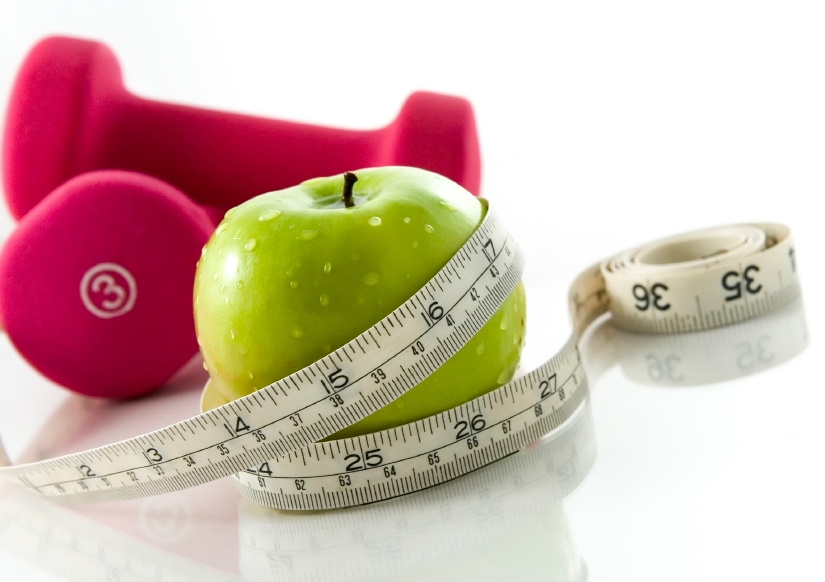
Do you recognize this situation?
Something seems to be wrong in your Supply Chain. Customer service isn’t where it should be and customers are complaining. Inventory is too high, consuming too much working capital. Waste levels are rising, eating away straight from your bottom line results.
You sit around the boardroom table with your leadership team and you decide to do a Supply Chain Health Check. You call a consultancy (preferably me of course) to do a health check. The consultancy comes in and roughly checks the following for you:
- Strategy, planning & execution health: a check on your Supply Chain strategy, the cascade to individual performance objectives, distribution network, KPI dashboards, reporting, inventory management, logistics execution, process definitions and supporting policies and procedures.
- IT health: a check on what systems enable your distribution network and inventory management, demand, supply & production planning, order to cash and purchase to pay processes.
- Meeting health: a check on meeting effectiveness, discipline, inputs and outputs, agenda, chairing, decisiveness, follow through and conflict resolution.
You get a nice presentation and a report back. You implement the solutions and after a while your supply chain seems to be working better. The customer stops complaining and the pressure moves away from the supply chain to another business area. Everybody moves on with business as usual. But here is the question:
Did your Supply Chain become really healthier?
According to the Oxford dictionary the definition of health is ‘the state of being free from illness or injury’. If we consider the above Supply Chain issues as illnesses or injury we indeed made the Supply Chain healthier.
The second Oxford definition is ‘a person’s mental or physical condition’. Although we can argue that a smoother Supply Chain reduces stress for team members, usually we didn’t spend any time with these people to understand if they actually perceive less stress, or have better mental condition.
Although I’ve heard many consultants say that ‘people and behaviours are most important’, this it often not part of their value proposition. With great surprise I’ve noticed over the years, that when you scratch the surface, you to discover that some consultants actually have no clue about project management, stakeholder management and change management, let alone about people and behaviours. Consultants pay this lip service because they know the leadership team they work with likes to hear this.
After just over 30 years of Supply Chain development, it is time to seriously address the people and behavioural side of supply chain. This thought isn’t new to me, as you can read in my 5 year old blog, the behavioural Supply Chain, which back then was published on the just launched Supply Chain Movement website.
Supply Chain people and behaviours
Now I run my own business, I can follow up on my philosophy. Of course I offer the normal project, stakeholder and change management services. But I also teamed up with the Value Chain academy, an organization that is pioneering global, scalable hard and soft Supply Chain education. On top of that I use two valid and reliable psychometric tools to measure individual and Supply Chain team thinking and behaviour. I’ll shortly describe them:
- Life Styles Inventory™:
The Life Styles Inventory™ (LSI), is a 240 question survey which is designed to bring constructive behavioural change. It provides for self-description and 360 degrees feedback from others. Research shows that constructive thinking and behaving has significant positive impact on personal well-being:
- Ability to manage stress (+39%)
- Life satisfaction (+26%)
- Workplace satisfaction (+21%)
Constructive thinking and behaving organizations outperform the least constructive organizations on:
- Motivation (+36%)
- Inter-unit coordination (+26%)
- External adaptability (+35%).
2. Mental Toughness:
Mentally Tough individuals perform better under pressure and stressors. Mental Toughness is measured with the MTQ48, a 48 question survey that measures a personal self-description on the attributes ofcommitment, control, challenge and confidence. Research shows that Mental Tough individuals:
- Show performance improvement.
- Display more positive behaviours.
- Sleep better and have less anxiety and stress.
- Accept change easier.
Mentally Tough teams outperform Mentally Sensitive teams on:
- Effective teamwork
- Decision making under stress.
- Transition and change readiness.
These type of individual well being and team performance impacts can’t be denied any more in a serious Supply Chain health check. In addition to the traditional Supply Chain health check described above, I use both tools in workshops and to individually coach managers and team members.
Constructive behaviours and Mental Toughness can be coached to improve. It is possible to help team members to increase awareness and adapt thinking, behaviours and routines to become less anxious, more confident and in the end, more effective. I also coach teams to understand each others behavioural preferences and reconcile between them. This creates understanding and supports conflict resolution.
Let’s stop playing lip service to people and behaviours in the supply chain. Let’s start helping individuals to develop effective behaviours that benefit their own well being as well as improve individual and team performance. Let’s start make real healthy Supply Chains.
—–
Niels worked for over 18 years in international Supply Chain positions and now runs his own business Truebridges in Melbourne Australia.
He is an AQR accredited master trainer in Mental Toughness and an accredited Life Styles Inventory coach. If you want to participate with your team in a Mental Toughness workshop, you can contact him atniels@truebridges.com or download the brochure here.